Weld Penetration Defects and Streamlining of Measurement and Inspection
Welding is commonly used in metal joining processes for products such as automobiles and airplanes. The quality of the weld can be assessed by measuring the dimensions of the weld penetration on a cross-section sample, and by inspecting defects such as insufficient penetration and joining failure.
KEYENCE's latest 4K Digital Microscope clearly expresses metal structure boundaries and defective areas even for low-contrast weld cross sections. Also, this microscope can quickly measure 2D and 3D dimensions, and automatically generate measurement results (such as images and values) in a report format, thereby achieving dramatic efficiency improvement.
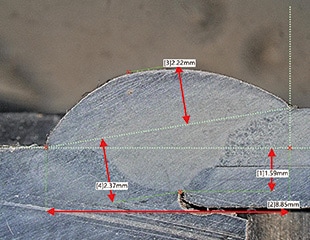
- Importance of Weld Penetration Inspection
- Welding Quality Related to Penetration
- Latest Examples of Using Microscopes to Streamline Weld Measurement and Inspection
- A 4K Microscope That Changes Weld Measurement and Inspection
Importance of Weld Penetration Inspection
Welding is commonly used in the joining of metallic components for products such as automobiles, airplanes, railroad cars, and ships. For automobiles, joining occurs mainly by means of various types of arc welding, resistance spot welding, and laser welding. These techniques are utilised on bodies, frames, engines, transmissions, chassis, and other such components to which stress is applied when the automobile is being driven. This puts importance on the strength design of welds and weld quality inspection through dimensional measurement of cross sections.
Mechanical properties and fractures of welds
The welds (weld beads and penetration) that join these base materials, while also being metallic material, include filler materials (such as welding rods and welding wires) that have been melted and solidified.
In typical arc welding, for example, metal structures continuously change not only in the weld metal but also in the parts of the base materials affected by the welding heat. Along with this change, the mechanical properties of the metal materials also change continuously. On the other hand, reinforcement, which is formed on the weld bead surface, has discontinuities. Discontinuity concentration leads to mechanical property deviation, thereby causing fractures due to stress concentration.
Strength design and welding quality
In strength design of metal products, materials are generally selected by assuming the load to be applied to the products and determining the load to be applied to each metallic material. Also, loads applied to welds of each material need be taken into account in strength design, thus setting a standard for welding quality that must achieved.
Therefore, it is important to inspect the welding quality on the basis of strength design by measuring, for example, the throat thickness (or throat cross section, the size of the weld bead cross section after welding), the leg length, and the penetration depth. The quality of welds can be evaluated through macroscopic measurement of cross sections after welding.
Welding Quality Related to Penetration
Penetration depth and penetration defects
The penetration depth is closely related to the joining strength. Any penetration defects on welds, such as inappropriate relationships between the penetration depth and base material, will greatly affect the quality and strength of welding. With butt welding as an example, the following describes typical penetration defects.
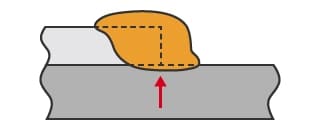
- Insufficient penetration
- A defect where the amount of penetration is insufficient compared to the required penetration depth due to factors such as insufficient application of heat to the molten metal. The figure shows an example of lap fillet welding. In butt welding, this defect easily occurs on the bottom of grooves. In the case of a thin plate tee (horizontal fillet) coupling, penetration is regarded as insufficient if the penetration depth is 20% or less of the thin plate.
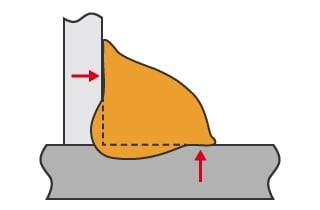
- Incomplete fusion
- A defect in which parts of the base metal have not been penetrated by the molten metal. The figure shows an example of a thin plate tee (horizontal fillet) coupling. This defect is caused, for example, by the insufficient application of heat to the molten metal and pre-flow of molten metal. In circumferential welding, it is also caused by the preceding and succeeding beads being transferred to lap welding before they have penetrated sufficiently.
Full penetration welding, partial penetration welding, and their strength
Different grooves also cause different patterns of penetration, leading to differences in the strength of welds.
- Full penetration welding
- Full penetration welding is a welding method in which the groove of the base material to be joined is united and embedded with molten joining materials (filler rod and welding wire), as with butt welding.
It can be said that full penetration welds are highly reliable in strength design as they have the same proof stress as the base material. On the other hand, they require high welding quality. Particular attention is required at the ends of welds to prevent defects such as undercut welds. It is also important to control and adjust reinforcement because stress concentrates on excessive reinforcement, causing cracking or other such problems.
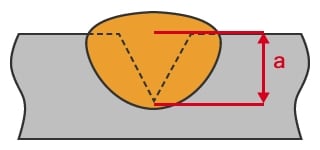
- Partial penetration welding
- Partial penetration welding is a method in which a partial groove is created on the base material. In this method, the base material is only welded partially, while full penetration welding welds the entire plate thickness of the base material. Although full penetration welding is used in general, partial penetration welding is required in some cases, such as where joined sections are intertwined due to the design and manufacturing of materials.
However, caution is required during partial penetration welding on locations to which bending moment or tensile force is applied because the welding strength of partial penetration welding is often not sufficient. Thus, the strength design of welds, as well as the measurement and inspection of whether dimensions of actual weld penetration such as throat thickness satisfy the design conditions, are all particularly important.
Latest Examples of Using Microscopes to Streamline Weld Measurement and Inspection
The cross sections of welds usually have low contrast between penetration and base material, so measurement using conventional microscopes is difficult and leads to variations between operators. Also, in the case of stereoscopic microscopes, it is necessary to visually check the scale and manually enter measured values.
In recent years, however, technological advancements in Digital Microscopes have solved the issues of conventional microscopes and have significantly changed the clarity of weld penetration and the efficiency of dimensional measurement. KEYENCE's VHX Series ultra-high-definition 4K Digital Microscope improves the efficiency of weld penetration inspection with clear images and dimensional measurement supported by the latest high-resolution lens, 4K CMOS, lighting innovations, and image processing technology.
4K high-resolution images that clearly capture the boundary between penetration and base material
The cross sections of welds sometimes make judgement and measurement difficult due to the low contrast of weld boundaries both for the penetration and the base material. Hence, these boundaries cannot be observed clearly with a conventional microscope.
The VHX Series 4K Digital Microscope can capture edges clearly with high-resolution 4K images. Even for the cross sections of lap fillet welding, whose boundary between weld metal and base material is hard to distinguish, it is now possible to quickly and distinctively observe clear boundary edges, differences in metal structures, and defective areas.
These observations eliminate confusion in conventional dimensional measurement of penetration and reduce work hours while improving inspection accuracy.
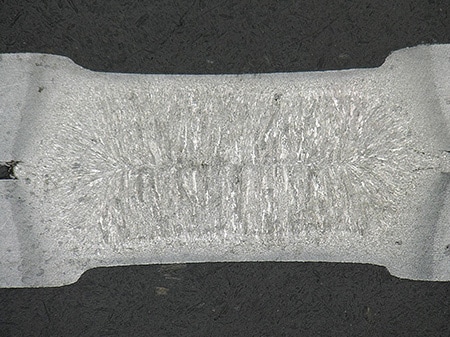
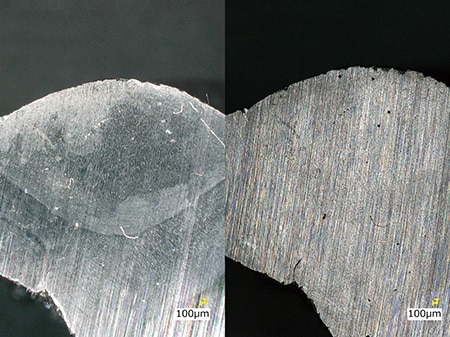
Left: high resolution/right: normal (30x)
Improving the dimensional measurement efficiency for welds
Dimensional measurement of weld cross sections is an important inspection related to strength and quality. However, with a conventional stereoscopic microscope, it is difficult to judge measurement points due to low contrast between the base material and the beads. Also, visual matching with memory and manual entry of the obtained values are required, resulting in the problems of human error and complicated operation.
With 4K high-resolution images on its monitor that can clearly represent weld boundaries, the VHX Series 4K Digital Microscope enables 2D dimensional measurement of items such as leg length, throat depth, and penetration depth through the easy operation of simply clicking the point to measure. You can complete even high-accuracy, submicron-order measurements easily and in a short time, thereby achieving significant work hour reductions.
Also, the latest automatic edge detection function prevents variations in measurement points between operators. Furthermore, a wide variety of inspection needs are satisfied thanks to the function that enables users to repeat dimensional measurements by selecting measured and saved data from an album.
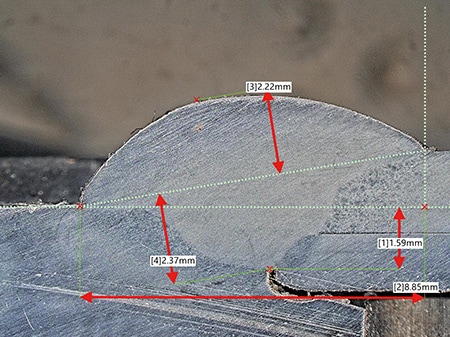
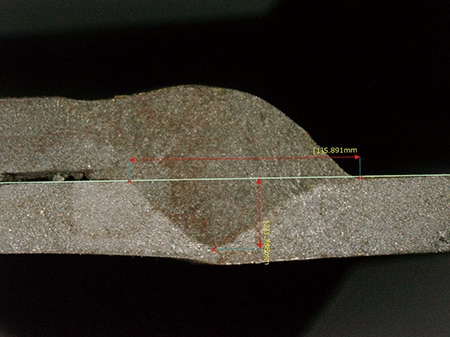
Weld penetration measurement
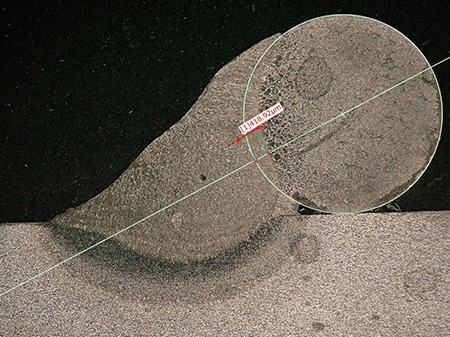
3D dimensional measurement and 3D shape of weld beads
Weld beads have continuous uneven shapes. If there are (discontinuous) defects on the bead surface such as insufficient reinforcement, overlap, undercut, pits, and cracking, the intended mechanical properties cannot be obtained and fractures may occur. Conventional microscopes, however, cannot bring the entire uneven bead surface into focus and cannot provide the height information required for evaluation of items such as reinforcement.
The VHX Series 4K Digital Microscope enables fully focused viewing and 3D dimensional measurement for targets that have uneven surfaces. Additionally, by displaying the 3D shape of weld beads, you can not only inspect the shape freely from various angles, but also measure the profile of any cross section. Because shapes and roughness can be analysed, you can also inspect spatters, cracks, and similar issues on the base material surface around weld beads.
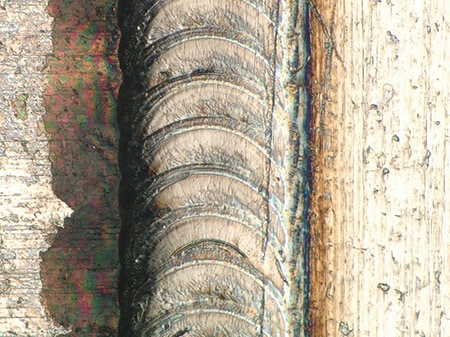
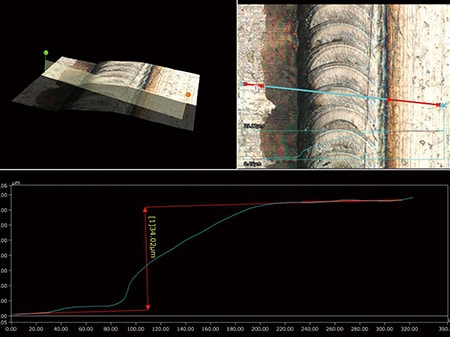
Instant creation of measurement and inspection reports
Conventionally, operators have had to deal with not only complicated measurement and inspection, but also the large workload that report creation entails.
The VHX Series 4K Digital Microscope is equipped with a report function. You can also install Excel on the VHX Series, just like a PC. Setting up templates in advance makes it possible to instantly enter not only magnified images, with the dimensions included, but also measured values and pass/fail judgements. These templates dramatically reduce the effort and man-hours required for report creation.
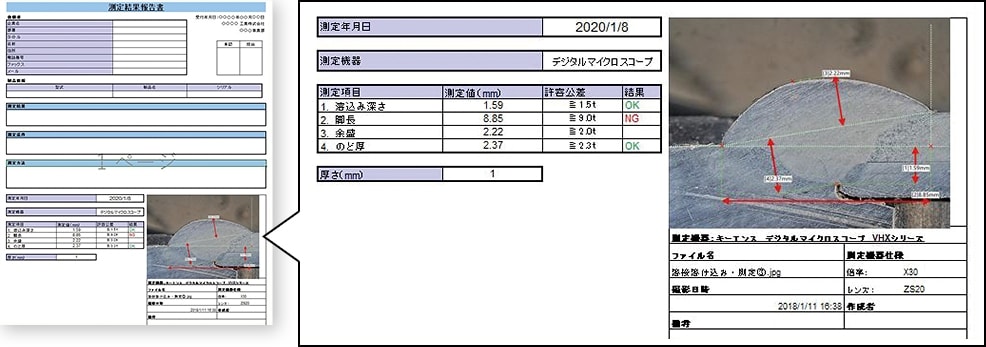
A 4K Microscope That Changes Weld Measurement and Inspection
The VHX Series is a powerful tool that solves problems in conventional measurement and inspection while improving work efficiency. It does so by way of its clarity that can be achieved only with 4K high-resolution images, acquisition of numeric data through high-accuracy measurement, and data saving and utilisation. It is equipped with many other advanced functions that were not conventionally available. In addition, many other functions are also provided to meet on-site requirements for speed and accuracy, such as a seamless zoom function that automatically changes the magnification between 20x and 6000x without lens replacement, the Optical Shadow Effect Mode and multi-lighting functions that help express the fine details of uneven surfaces clearly, and automatic templates for repeated measurements.
For additional product info or inquiries, click the buttons below.