[Logistics Industry]
This section introduces handheld mobile computer application examples in the logistics industry. Actual examples will be used to explain the problems in various processes in the logistics industry and the advantages provided by installing handheld mobile computers.
- Logistics
- Problems in Logistics
- Solving Problems by Installing Handheld Mobile Computers
- Typical Processes and Manufacturing Flow (Warehouses/Distribution Centres)
- Advantages Provided by Installing Handheld Mobile Computers in Various Processes
- Typical Processes and Manufacturing Flow (Package Transportation)
- Improving Operation With Character Recognition Handheld Mobile Computers
Logistics
Logistics is the flow of items. The entire flow that contains all the processes used to bring a company's products to its consumers is referred to as logistics. Logistics contains aspects such as distribution centres, warehouses, and other such storage locations; delivery by large trucks; transportation by ship, airplane, and other such means; and logistics systems used to deliver products. Compared to the manufacturing industry, there are many more processes in which work is performed by hand. This results in the trend that it is easy for problems such as picking mistakes and shipping errors to occur in the logistics industry.
Problems in Logistics
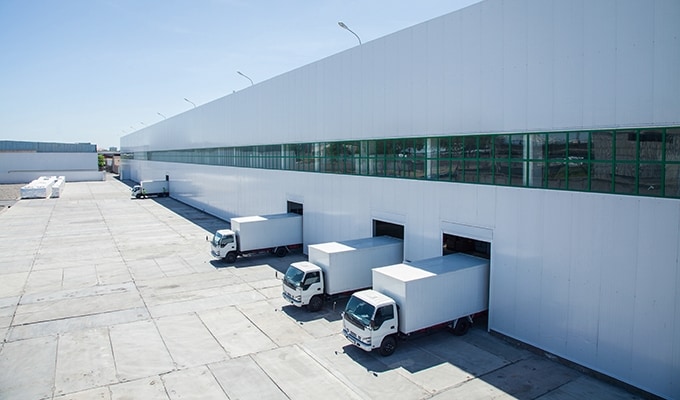
Even though there has been a major shift toward IT in industries at large, a large amount of work at logistics worksites, such as inspections and inventory management, is still performed visually or otherwise manually by operators. This leads to the characteristic of logistics that it is easy for user-caused errors to occur and for work to be inefficient. Especially during receiving and shipping inspections, lists and products are verified visually, so it is easy for items to be missed and for the entry of data for some items to be forgotten. This means that it is easy for inventory management to be thrown off. In recent years, the rise of online shopping has led to a sudden increase in the number of packages handled, so there are pressing needs for warehouses and distribution centres to become more efficient.
The major role of the logistics industry—its warehouses, delivery centres, and similar facilities—is to be the middleman between producers and consumers so products reach the people and companies that need them when they need them. However, to do this it is necessary for logistics worksites to strictly manage the inventory situation and the processes from receiving to shipping. Yet, while machinery and automation are used to a high degree at worksites in the manufacturing industry, the processes from receiving to shipping in logistics still mainly rely on the eyes and hands of operators, which leads to mistakes such as erroneous shipments occurring on a daily basis.
Solving Problems by Installing Handheld Mobile Computers
Handheld mobile computers can be used in operations such as receiving and shipping inspections to obtain accuracy that does not rely on visual checks and the recording of data on paper. If barcodes or 2D codes are affixed to products when they are received, common barcodes or 2D codes can be used for everything from management within the warehouse/distribution centre to shipping to achieve accurate product management. Also, handheld mobile computers can be used during picking to enable anyone to perform work with the same accuracy and speed regardless of experience and skill levels.
Typical Processes and Manufacturing Flow (Warehouses/Distribution Centres)
This section explains detailed handheld mobile computer installation examples grouped by process during logistics. First, the typical processes and manufacturing flow for warehouses/distribution centres are shown below.
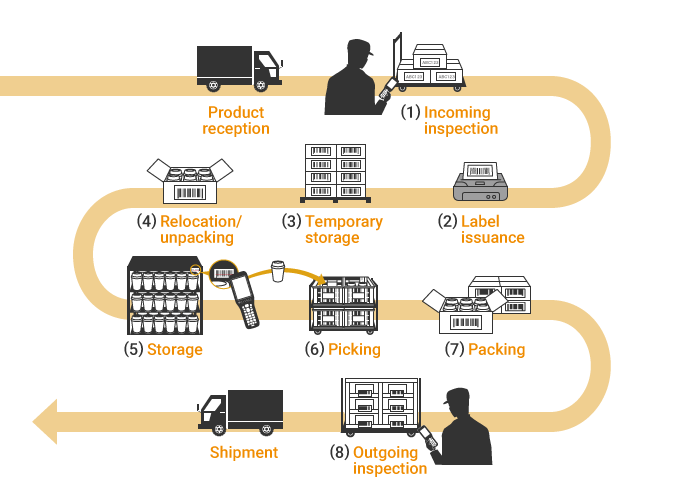
Advantages Provided by Installing Handheld Mobile Computers in Various Processes
This section explains the advantages of installing handheld mobile computers and actual application examples for the typical processes in warehouses/distribution centres.
Inspection of receiving goods
During the inspection of receiving goods, the delivered goods and the delivery slip that was sent together with the goods are verified to check that there are no problems with the product numbers and quantities and the goods are inspected for damage and problems in quality. If the inspection of receiving goods is performed visually, it is inevitable that some items be missed or read incorrectly, that the recording of some items in the ledger be forgotten, or that other similar errors occur. Mistakes that occur at this stage will be carried through to shelving and picking and may finally result in erroneous shipments. Handheld mobile computers can be used in this inspection of receiving goods to eliminate the majority of user-caused errors and thereby prevent erroneous shipments.
Label issuance
If barcodes are not affixed to products and packages when they are received, the shelving work becomes complicated, which makes it easier for operators to mistake the storage location. This mistake occurring leads to confusion in the later process of picking work. Installing handheld mobile computers and affixing on each package barcode labels issued from the data of the inspection of receiving goods enables efficient shelving and inventory management.
Shelving
Affixing to cases and racks the barcode labels created in the previous process while performing shelving increases the efficiency of the shelving work and also makes it easy to check the shelving (to verify data).
Picking
Operators can use handheld mobile computers to simply scan the picking lists and immediately find the shelf on which the product is stored. This reduces unnecessary movement and makes the work more efficient. The barcodes affixed on the shelves can be verified against the products, which prevents picking mistakes. Furthermore, there is no need for operators to rely on their memory and experience, so even inexperienced staff members can be assigned to worksites.
Shipping inspection
The major cause of shipping inspection mistakes is operators performing these inspections visually while viewing picking lists and shipping instructions. Regarding this point, barcode inspections with handheld mobile computers dramatically improve the verification accuracy. Also, integration with the system means that when the information of the shipping checked products and their quantities is scanned, this information is fed back into the system in real time. Therefore, it is possible to determine accurate inventory data on the spot.
Typical Processes and Manufacturing Flow (Package Transportation)
A common problem in package transportation, especially in home delivery work, is cargo loss. The article in question remaining lost is a major problem, but even if cargo that was temporarily lost is found, failing to deliver it to the consignee on schedule will result in complaints and will develop into problems regarding trust in the service. If handheld mobile computers are used to create a package tracking database and if all processes from pickup to completion of delivery are managed in a centralised manner, the place where a package was lost can be brought to light immediately.
A package tracking database that utilises handheld mobile computers can be used for more than just avoiding cargo loss. The information sent from the handheld mobile computers in all the processes from pickup to completion of delivery can be collected, so the delivery route and driver assignments can be optimised in the event of waste in the intermediate routes and similar issues, thereby promoting the conversion to more efficient work. Also, consignees (users) just have to search online for their tracking numbers to obtain the statuses of the packages being delivered to them. Furthermore, the delivery date and time can be changed on the home delivery vendor's website if necessary. In this way, the package tracking database is also a tool that improves customer service.
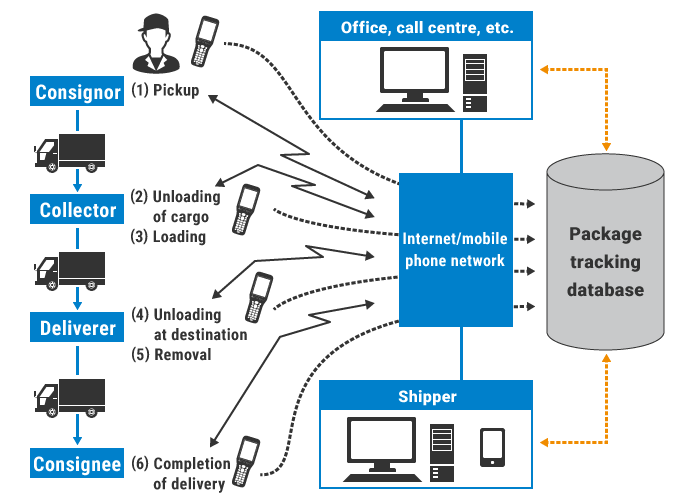
Pickup
The drivers who work for the office perform cargo booking by going around to convenience stores and other such service points and picking up the packages requested by the consignors. It is also possible to pick up packages directly from consignors. At this time, a tracking barcode is printed on the slip affixed to the package, and the driver scans each barcode with a handheld mobile computer whenever a new package is picked up. This data is automatically sent to headquarters over a mobile phone network. Also, a classification label that indicates the delivery destination area is created according to this data and is printed from a compact printer accessed from the handheld mobile computer to affix it to the package.
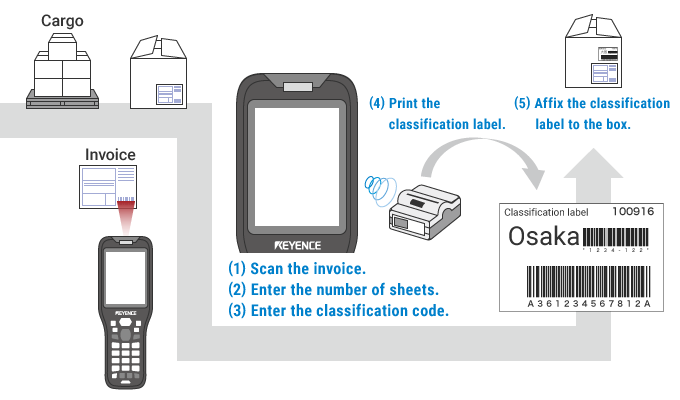
Unloading of cargo
The cargo that has been picked up is unloaded at the corresponding office. The barcodes are also scanned here with handheld mobile computers to verify them against the data from the time of pickup, checking whether the amount of unloaded cargo is correct. If cargo loss has occurred, it can be detected at this point.
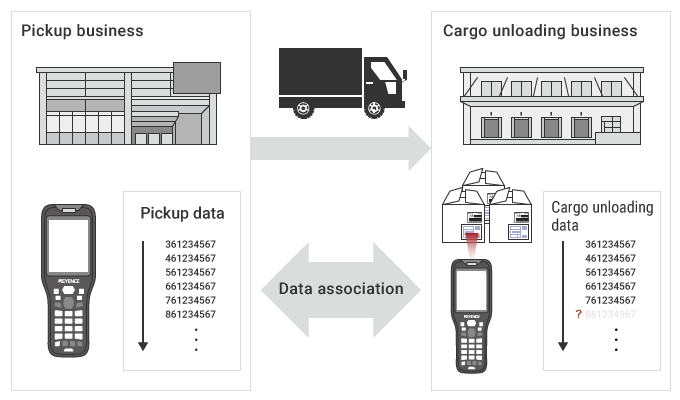
Loading
The barcodes on the invoices and classification labels of the unloaded cargo are scanned again with handheld mobile computers, and the packages are then grouped according to delivery destination area. Once preparations are complete, the packages are loaded onto trucks, which then depart for their destinations. Absolutely no handwritten records are necessary for the management of packages. All data is entered into the system by scanning codes with handheld mobile computers, so no user-caused errors such as reading data incorrectly and forgetting to write down certain items occur. Of course, major improvements in the efficiency of the work can also be obtained.
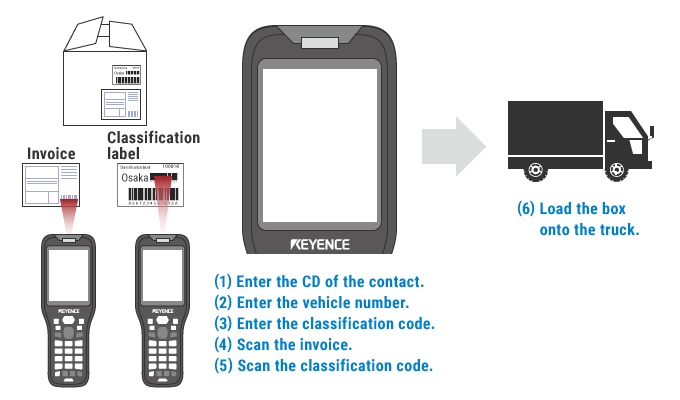
Unloading at destination
At the destination, packages are unloaded from the truck and the barcodes on the invoices are scanned again with a handheld mobile computer to verify them against the data from the time of pickup, checking that the amount of packages is correct and that no cargo loss has occurred.
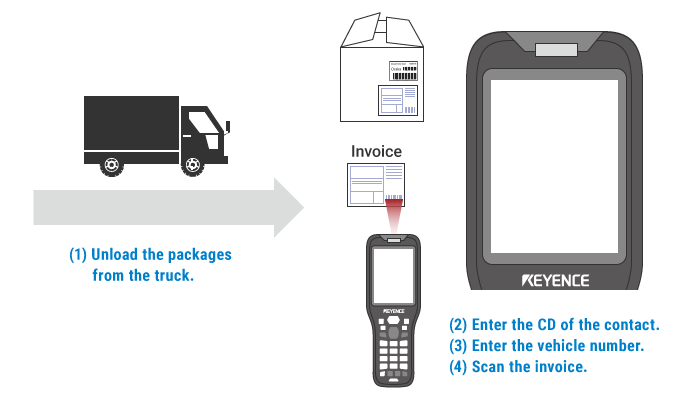
Removal
If there are no problems with the status of the packages unloaded at the destination, the operation becomes “removal,” and the packages are delivered to the consignee. If the consignee changes the delivery time, a message is immediately sent to the driver's handheld mobile computer.
Completion of delivery
After the driver arrives at the consignee's location and delivers the packages as scheduled, the driver scans the invoice and notifies headquarters of the completion of delivery. Because handheld mobile computer data is sent for each operation, headquarters can perform package tracking management in nearly real time.
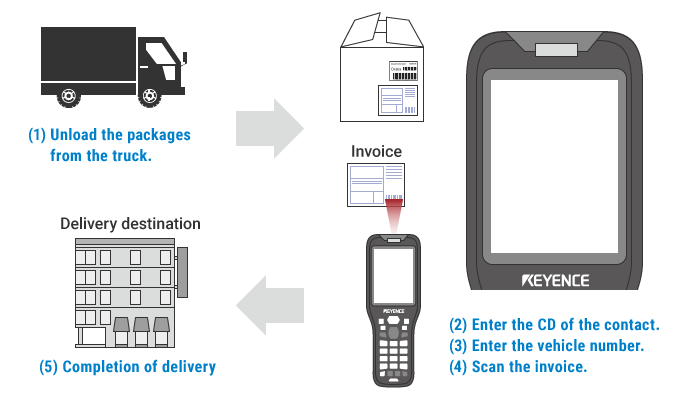
Improving Operation With Character Recognition Handheld Mobile Computers
At logistic operation area, sometimes the product slip during warehousing has no barcode and only has the serial number and lot number. Normally, visual inspections are performed if there is no barcode, but this poses the risk of similar character strings being misread. Mistakes may also occur during later management when making handwritten memos of the serial number and lot number or when entering this information into a PC. Furthermore, the serial number and lot number will also be a hassle in later management. Switching from visual inspections to inspections with handheld mobile computers that support optical character recognition (OCR) can greatly reduce problems such as misread and incorrect data entry, which decreases the hassle involved in product management. KEYENCE's BT Series of handheld mobile computers supports optical character recognition (OCR), so these devices are very effective in situations such as that shown below.
On-site label issuance
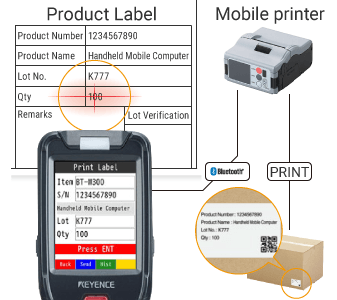
The misread that occurs during visual inspections can be prevented by using handheld mobile computers to read the serial number and lot number text of parts and raw materials during warehousing. Furthermore, converting the read data into a barcode, using a mobile printer to print a label with the barcode, and sticking the label to the package enables barcode management in later processes. This makes it possible to start using barcodes in an in-house system easily and inexpensively.
Conventional
- Visual check and manual entry into a PC
-
- A: Manually enter the product slip text.
- B: Issue a label with a barcode.
- C: Stick the label to the package.
Improvement
- Just scan the text to easily print a label from the printer.
-
- A: Read the target with the handheld mobile computer.
- B: Issue a label with a barcode from a mobile printer.
- C: Stick the label to the package.