Pokayoke (Error-proofing)
Mechanisms for detecting or preventing the generation of defects caused by careless mistakes, which are unavoidable at manufacturing worksites, is referred to as pokayoke (error-proofing). This section introduces items such as basic knowledge pertaining to careless mistakes and pokayoke (error-proofing), the way to use a handheld mobile computer system to perform pokayoke (error-proofing) and the advantages of doing so, how to install handheld mobile computers, and the flow for operation of handheld mobile computers.
- What Is Pokayoke (Error-proofing)?
- Pokayoke (Error-proofing) With Handheld Mobile Computers
- Advantages Provided by Handheld Mobile Computers
What Is Pokayoke (Error-proofing)?
User-caused errors occur at manufacturing worksites and lead to defects.
These user-caused operation errors are generally referred to as careless mistakes. The mechanisms for preventing the occurrence of careless mistakes and for preventing defective products from mixing in with good ones even if careless mistakes occur are referred to as pokayoke (error-proofing).
These mechanisms are separated into defect prevention (error stoppage, mistake restrictions, and prevention alarms) and defect detection (defect stoppage, flow restrictions, and occurrence alarms). It is also possible to identify the causes of defects and the processes in which they occurred, which makes it possible to develop improvement strategies for preventing the reoccurrence of defects.
In summary, pokayoke (error-proofing) refers to the mechanisms for notifying users of the occurrence of defects, preventing defective products from mixing with good ones in the rare event that defects occur, and preventing the reoccurrence of defects.
Pokayoke (Error-proofing) With Handheld Mobile Computers
There are various causes of careless mistakes at manufacturing worksites. Just a few examples are incorrectly reading product numbers, taking the wrong part, making mistakes in the setting of moulds and jigs, and making mistakes in the blending of raw materials. Careless mistakes such as these can be prevented by thoroughly performing verification with handheld mobile computers. This section introduces pokayoke (error-proofing) using handheld mobile computers.
Pokayoke (error-proofing) with shipping inspection and actual/sign product verification
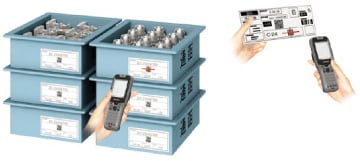
The possibilities of incorrect parts being shipped and part shortages occurring during shipping can be reduced to nearly zero by performing a duplicate check in which the barcodes and 2D codes on the customer sign and the in-house sign are read. The pokayoke (error-proofing) effect can be further increased by performing three-point verification visually by displaying the target image on the LCD of the handheld mobile computer.
Shelfing pokayoke (error-proofing) when stocking/restocking parts
To prevent accidental introduction of items onto shelves when stocking/restocking parts and raw materials, affix item labels (barcodes) to parts and product number barcodes to the part shelves, and then use handheld mobile computers to verify both barcodes. With visual inspection, it is possible that similar parts will be introduced accidentally, but management with barcodes can prevent careless mistakes when shelfing parts.
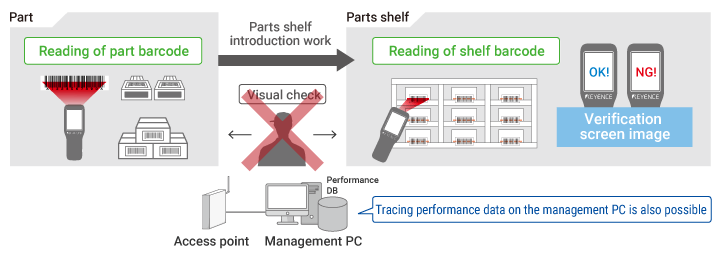
Recipe checks when blending/compounding raw materials
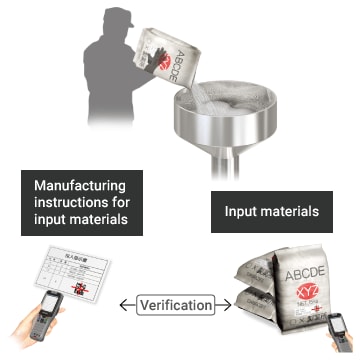
When beginning production or during tool changeovers, blending and compounding mistakes can be prevented by verifying the manufacturing instructions against the barcode of the raw materials to be inserted.
Checking the setting of moulds and jigs
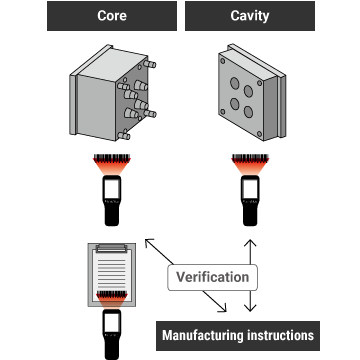
During production of small lots of a wide variety of products, tool changeovers occur frequently and similar moulds and jigs may be used. This may lead to mistakes in the setting of moulds and jigs. Such mistakes can be prevented by affixing barcodes to moulds and jigs in advance and verifying the manufacturing instructions against the moulds and jigs.
Using OCR to verify on job card and production card
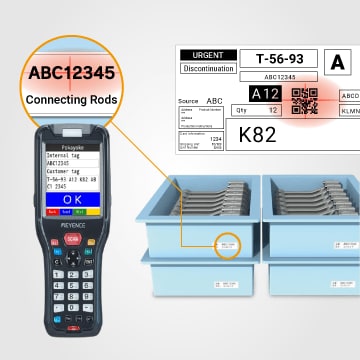
Handheld mobile computers that support optical character recognition (OCR) can read text such as serial numbers and lot numbers. Using optical character recognition to read a product slip and verify the data against the product improves both the accuracy and speed over that of visual checks. In addition to eliminating mistakes, this is also effective in improving work efficiency. KEYENCE's BT Series of handheld mobile computers includes OCR-applicable models.
Advantages Provided by Handheld Mobile Computers
This section introduces the advantages of installing handheld mobile computers for pokayoke (error-proofing).
Eliminating careless mistakes caused by taking the wrong product among similar ones
As the number of products whose outer appearances are similar increases, these products may look the same to inexperienced operators. Careless mistakes caused by taking the wrong product can be eliminated by affixing barcodes or 2D codes to products and having operators read these codes with handheld mobile computers during confirmation.
Able to output data and signals to the control device
By outputting the data read by the handheld mobile computer to an indicator, interlock, or other such control device, notification of an error occurring when verification fails can be provided with the indicator and the interlock can be released when verification passes. This makes it possible to eliminate careless mistakes in various operations.
Sending work data to a PC or server in real time
Data read with a handheld mobile computer can be sent to a PC or server in real time. This makes it possible to monitor the occurrences of careless mistakes from the headquarters or an office. Notifications of careless mistakes are given in real time and the work information from preprocessing can also be checked, so this is effective in identifying the causes of careless mistakes.